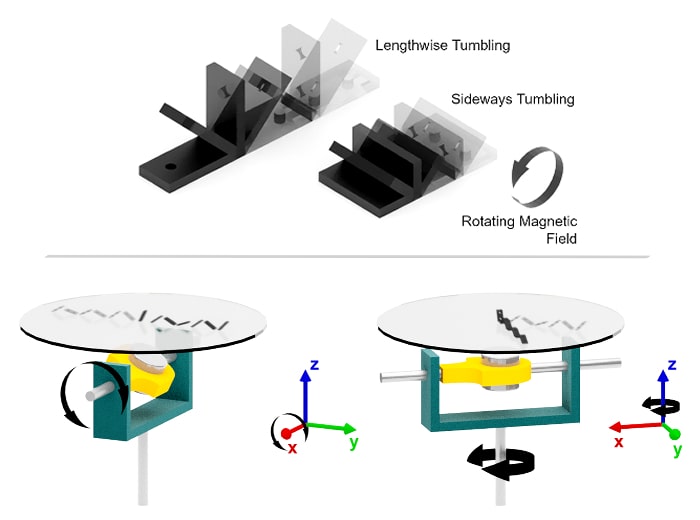
Tumbling Mode/Magnet Manipulator Figures
Images modeled and rendered in Blender to visualize two primary modes of tumbling locomotion and degrees of freedom of motorized magnet manipulator. Used as part of recent research paper submission.
I spent the last three years working on magnetic tumbling microrobots - tiny polymeric blocks that locomote by tumbling end-over-end. Each microrobot contains embedded neodymium particles that allow for wireless manipulation by a rotating magnetic field. Nontoxic and smaller than a grain of sand, these microrobots can be placed inside the human body for noninvasive biomedical applications, such as targeted drug delivery and disease detection. Versatile tumbling locomotion allows for controllable movement in many different environments - over bumpy terrain, wet and dry conditions, and steep inclines.
I drew inspiration from past and current research to continuously improve the tumbling microrobot design. I reduced the number of fabrication steps required, improved the magnetic response fivefold, decreased the minimum field strength requirements, and introduced the idea of using elastomeric materials with non-uniform alignment. Being responsible for experimentation as well as design, I developed various test setups and custom features/fixtures for benchmarking the microrobot's performance. Limited resources meant constant collaboration with other labs and creative approaches to realizing necessary functionality.
One of the biggest hurdles for experimental setup was designing and building a motorized magnet manipulator. The tight size requirements of several ultrasound imaging experiments limited use of the bulky, pre-existing MagnebotiX system for generating magnetic fields. A smaller, more portable device was needed to actuate the microrobots. Three iterations of this device were ultimately created as the scope of the project kept scaling up, with each iteration becoming increasingly complex. From a tiny hand crank version to a two degree-of-freedom version with PID control, each variant incorporated 3D-printed parts to reduce fabrication time, avoid machining difficult geometry, and minimize the use of magnetic material, which could interfere with magnet movement and distort the output field.
Performance predictions and planning were essential to the project, as rapid prototyping was difficult for the tumbling microrobots. Each microrobot required photolithography, curing, and magnetization steps that were costly and took several combined hours to carry out. New designs required a new photolithography mask that needed to be ordered at least a week in advance. To work around these limitations, I modeled the static and dynamic motion behavior of the microrobot in MATLAB to simulate its performance, verifying the model with past experimental data. Using the simulation tool, I could optimize the microrobot design before physical fabrication steps were carried out. I experimented with several commerical and open-source simulation engines as well, picking up C and Python coding along the way. CAD design in AutoCAD and SolidWorks was used extensively to generate .stl files for fixtures/custom parts, create new photolithography masks, and double-check calculated inertia/mass values.
A large part of research is sharing results and communicating new ideas. My time at Purdue's Multi-Scale Robotics and Automation Lab resulted in six publications, with two more ongoing submissions. Each new article required a different style of writing from the last - with an article in American Scientist being furthest from the norm. Here, I was challenged to create a compelling story for microrobotics and make dense research content more approachable for the unfamiliar reader. Along with technical writing, I presented my work in person on many occasions to engineering professionals and peers - at the 2018 Midwest Robotics Workshop, on guided lab tours, at the 2019 Advancing Health Conference at IUPUI, and during my thesis defense. I volunteered twice at Purdue's annual NanoDays festival, where K-12 students learn about nanotechnology, and I co-taught swarm robotics last year at a local summer camp using VEX and Lego EV3 sets. Having come from an additional year and a half of university teaching assistantships, I'm familiar with explaining complicated ideas, doing live demos and examples, and making tutorials/materials to aid understanding.
My favorite way of sharing ideas is through images - anything visual. Barring text labels and legends, visual media transcends any language barriers in the increasingly global world. Whether it's a research paper, email update, or presentation, I love opportunities for creating and incorporating graphics in my message. Below is a collection of several images, figures, and slides I have worked on over the years. Feel free to click around the gallery to see larger and more in-depth images. I am particularly proud of the Micromachines cover, which was selected as the official journal cover for its April 2019 issue.
Images modeled and rendered in Blender to visualize two primary modes of tumbling locomotion and degrees of freedom of motorized magnet manipulator. Used as part of recent research paper submission.
Highlights key components of alginate capsule research paper. Composed of several stock images, experiment photos, and a Blender depiction of one of the key experiments (pushing a T-shaped structure using a group of rotating capsules).
Hand-drawn images used to provide visual examples of content discussed in thesis presentation and help with audience understanding.
Slides used to introduce middle school and high school students to camp schedule and content. Includes guided explanation of camp's two main challenges.
Graphics used in senior design poster to explain functionality in step-by-step manner. Made from a mixture of SolidWorks and stylized SketchUp renders.
Two story sequences depicting shortcomings of conventional smartphone technology. In both cases, a haptic alternative (touch-based notifications and navigation) would allow the user to keep his/her eyes on the road.
Promotional material created during time in marketing committee at Purdue's SASE chapter.
Before doing research full-time, I worked on several engineering projects as an undergraduate student. These projects focused on finding market gaps and developing functional prototypes to meet the demand. Machining, mechanical design, and mechatronics know-how were essential to making this possible.
Pushing the tolerance and feature size limits of a Stratasys Mojo FDM printer, this ABS structure with several moving components was created from a single print job - no assembly required. It was created for highlighting how 3D printers can fabricate objects that would normally be infeasible to make using traditional machining methods.
Warehouse logistics robot prototype capable of transporting inventory (up to 30 lb) stored in totes between shelves (up to 6' in height). All structural components were machined from steel, aluminum, and nylon stock material in order to stay within the allocated budget. Cameras, IR sensors, bump sensors, and an on-board myRIO microcontroller were installed to allow for potential automation in the future. A bluetooth module allowed for wireless manual control.
Exploring potential of cost-effective programmable haptics device. Functional mockup contained five circular DC motors to provide haptic feedback to user. Motors vibrated in different spatial arrangements and intensities to indicate different instructions. 12 participants were able to follow a predetermined path using haptic cues.
Prototype of functional components of an egg-decorating toy. Motorized spindle/track makes creating striped designs easier and spring-loaded pen holder allows for consistent pressure of pen/paintbrush on egg. Gear system makes control of the pen's orientation more precise.
Budget, 3D-printed modular robot based off of pre-existing SMORES design. Changes included simplified assembly with only two screws and press fit components.
I make an effort to maintain a diverse skillset and constantly try new things. I think many of the most innovative ideas come from combining seemingly unrelated things from different specialties. In addition to general mechatronics knowledge, I'm well-acquainted with several additional tools used by researchers, programmers, and artists alike.
Static and dynamic simulation of microrobot behavior using numerical equations of motion in MATLAB.
Incorporating CAD models, drawings, and renders into various projects using SolidWorks, Creo Parametric, and AutoCAD.
Printing objects using various MakerBot, LulzBot, Formlab, Stratasys, EnvisionTEC, and Ultimaker devices and familiar with their capabilities and limitations.
Proficiency with general milling and drilling operations on wood and metal parts. Basic knowledge of lathe and CNC operations.
Developing experiment procedure and metrics for evaluating microrobot performance, as well as fabricating custom fixtures and terrains. Frequent use of ImageJ to analyze results.
Frequent collaboration with additional labs from Purdue University's School of Biomedical Engineering, the Illinois Institute of Technology, and Stony Brook University to expand project scope beyond lab resources.
Programming microcontroller routines and drivers extensively in C, with additional C/Python coding for various simulation packages.
Basic web design and additional functionality using JavaScript. Working example is dynamic undo counter used as a stream widget.
Meeting research journal writing style/format requirements and frequently making use of collaborative document writing in Overleaf.
Proficiency with Adobe Photoshop and Clip Studio Paint for generating explanatory illustrations.
Creating realistic and stylized renders from custom models in Blender and SketchUp for highlighting key concepts.
Supplementary video content for several research papers. Needing to negotiate differing file formats, framerates, resolutions, and aspect ratios while conforming to journal requirements.
I'm excited to explore and share new ideas in the growing world of product design. I hope we can work together to find tomorrow's game-changing discoveries.